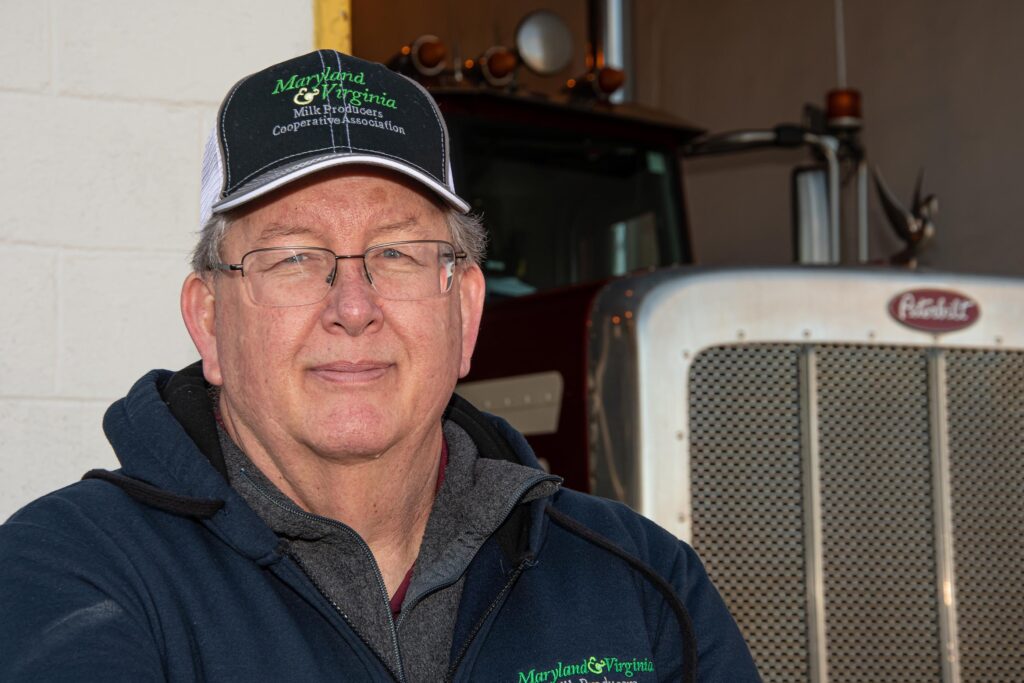
Where Waldo Wanders
It’s not a beanie with a red plume and stripe. But the cap that Maryland & Virginia Milk Producers Field Representative Carl Espenshade chooses to wear is his own signature style — just like the eponymous children’s puzzle book character Waldo.
The series’ title – ‘Where’s Waldo’ — was also the inspiration for the name of the special assignment that was crafted by Member Services team to better engage with the process of getting milk from farm to plant.
Enter Espenshade (and his MDVA cap), who came to Maryland & Virginia in 2021 after 25 years in various regulatory capacities at the Pennsylvania Department of Agriculture (PDA). He fit the mold perfectly as someone who could identify potential weak spots in the process and offer potential corrective actions.
We had found our very own Waldo.
Process, Procedure, and Protection

The initiative, now about a year-and-a-half old, sees Espenshade meeting with haulers on the farm, riding along with them on their routes, or catching them at both MDVA-owned and third-party plants. While visiting with them, he reviews their inspection records, sample-keeping procedures, decorum, and overall cleanliness.
Espenshade says ‘Where’s Waldo’ helps protect both the member and the hauler. For the member, it offers an accountability process that can make farms confident in the handling of their product and its corresponding quality after it leaves the farm. For the hauler, it helps offer continuing education to drivers as well as a layer of extra quality control on top of their own procedures.
“Unfortunately, the easy finger pointing is ‘the driver did it.’ That’s not always the case,” says Espenshade. “We want to be able to solve that issue and ‘Where’s Waldo’ helps redirect where we need to look when things go wrong.”
And of course, for Maryland & Virginia’s customer, it assures that they get only top-notch milk every time.
Where ‘Waldo’ Began
Espenshade is uniquely qualified to offer analysis on procedures. He inspected milk plants, haulers, and farms for PDA as a state rating officer for 15 years before retiring in 2021. Before that he inspected livestock for PDA for ten years.
Milk has always been a highly scrutinized product. Espenshade recalled his time at PDA when he inspected a plant that made both milk cartons and wrappers for a high-profile candy.
“The milk carton printer had to be spotless,” he said. “The candy printer did not have the same guidelines, even though you’d think with food, there would be similar standards across the board. That’s not always the case.”
Espenshade is married and has seven kids and five grandchildren. He still lives in Pennsylvania, calling Wrightsville home. He cites his family as one of the reasons he’s spent much of his life protecting the dairy supply chain.
“I like dairy products. I want to make sure that when we sell our product that it’s safe for my family and yours,” he says. “No one wants to get sick from food poisoning. No one wants to get an illness from a pathogen that can devastate your life. We’re working to make sure that doesn’t happen with something that is preventable.”
‘Waldo’s Wandering Nature
There’s not really a playbook that guides ‘Where’s Waldo’ Espenshade says. He’s been extended the freedom to dig in when he can find a free moment in his already busy schedule as a field representative.
“I might come on a Sunday,” he says of his observation schedule. “I might come on a holiday. I might come for 10 minutes, or I might come for 10 hours.”
In the plants, he reviews the receiver’s procedures, always ensuring that high-quality standards are being met. Some of the important things Espenshade looks at in the receiving process is the correct handling of samples and cleaning procedures of tanker lids, pumps and hoses.
For haulers, Espenshade continuously underscores the need to have sanitizer solution for the dipper, which is what haulers use to collect milk samples from the tank prior to loading.
“If you have a four-hour route, you don’t want that first farm’s milk still on the dipper,” he says. “Not sanitizing equipment can impact milk quality, which impacts the pay of our farmers. We must hold everyone to those high standards so that every producer gets the quality results they deserve.”
The relationship between Maryland & Virginia and our haulers is strong, but even the strongest bonds might not appreciate one poking into another’s business. Espenshade says that hasn’t been the case with his conversational approach to his audits.
“Just because I’m an inspector doesn’t mean I know everything. And for the drivers, just because we’ve been trained once doesn’t mean we are trained for life. Continuing education must happen.”
Where ‘Waldo’ Will Go
Espenshade says he believes MDVA is the only cooperative doing something like this in our market today.
“We’re ahead of the game on this,” he says.
The program has been so successful that one of Maryland & Virginia’s third-party raw milk customers recently asked Carl to come visit their facility and review policies and procedures. Espenshade spent a day at their plant and offered solutions that helped them improve quality.
“Getting a third set of eyes is great,” he says. “I was able to offer them some solutions that they hadn’t even thought about. Every person in the dairy supply chain matters when it comes to milk quality. The farmer, the hauler, plant employees, distributors, and retailers all have a role to play in producing safe milk – and we can’t have a break in the chain. “